Environmental
As a leader in the sector, it is vital that we look beyond simply what happens when a car visits a centre for new tyres or other components. We consider not only the elements of our upstream supply chain but also what happens to the products we supply once their useful life on vehicles has come to an end.
Production
ETEL is an integral part of PROJECT TREE, an innovative programme which aims to protect the rainforests of Indonesia by helping meet the demand for natural rubber through sustainable and ethical methods.
The supply of natural rubber used in tyres, among many other applications, relies on thousands of farmers who tap the rubber trees on their small holdings and sell the raw latex to collectors, dealers and processers. The project is designed to bring transparency to this natural rubber supply chain, encouraging sustainable practices while at the same time protecting the livelihoods of the smallholders dependent on rubber for their family’s income.
Under the PROJECT TREE scheme, a portion of the purchase price of each supported tyre is allocated to the farmers supported by the programme. In the pilot phase, Kwik Fit saw sales of PROJECT TREE tyres exceed expectations, in spite of the small cost premium. With PROJECT TREE tyres now available from Pirelli, Hankook and Continental, Kwik Fit expects to sell over 150,000 PROJECT TREE tyres this year.
PROJECT TREE has developed a proprietary traceability system which uses blockchain technology to track and inspect the supply chain. This software is designed to help prevent rubber entering the system from inside the conservation area.
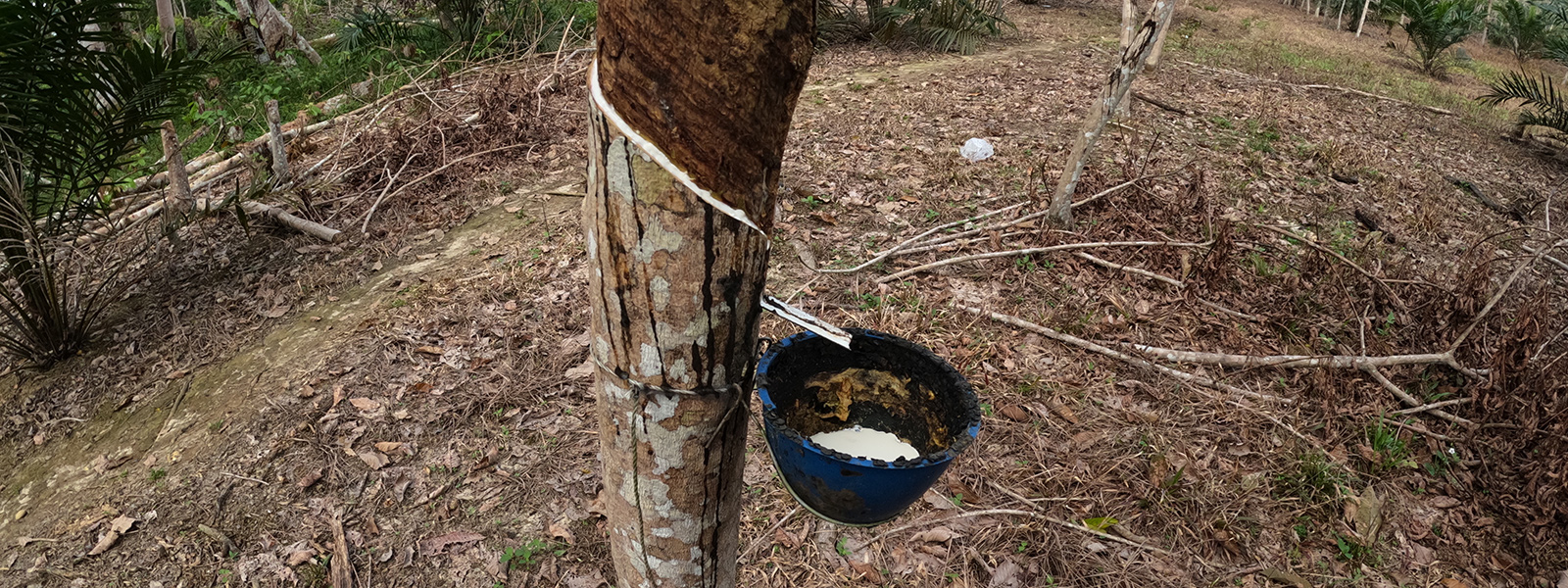
A historic problem in natural rubber production has been that increases in demand have seen communities clearing land, in some cases illegally, in order to plant new rubber trees. Not only is this land clearance a serious issue, but it has often been counter-productive. With a rubber tree taking around six years before they can be tapped, the spike in demand may have disappeared by the time these newly planted trees are producing latex, resulting in oversupply.
The PROJECT TREE team is working with communities by offering incentives and training to help improve yields on existing land. This will enable farmers to increase production more quickly than planting new trees and will also help halt the loss of biodiversity. As many smallholders do not have bank accounts, the project will operate pool accounts providing farmers with access to education, tools and fertilisers where required.
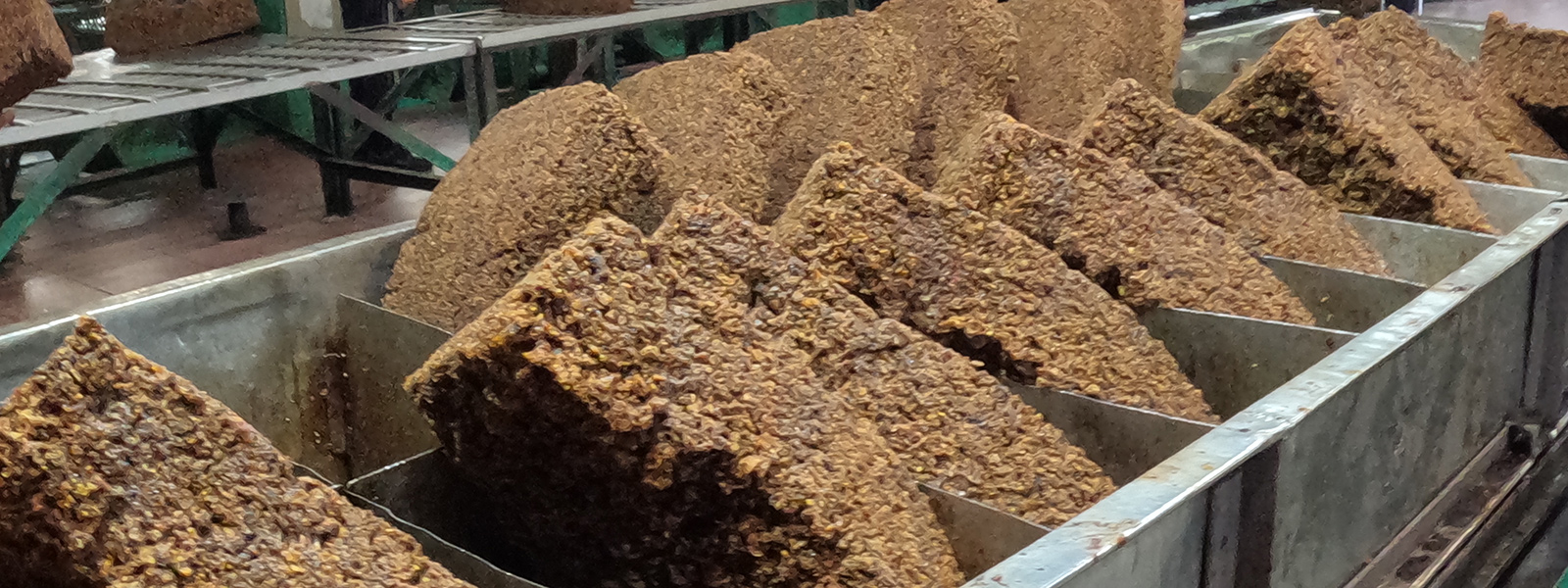
The project has been developed by ITOCHU, ETEL’s parent company, through its rubber producing subsidiary PT. Aneka Bumi Pratama (ABP). Partners in the project include Proforest, a global organisation focused on responsible sourcing and production of agricultural and forest commodities and SNV, a not-for-profit international development organisation that works across sectors of Agriculture, Energy and Water, Sanitation and Hygiene (WASH), and seeks to make a lasting difference in the lives of people living in poverty through sustainable development.
For more information and news on the progress of PROJECT TREE visit our dedicated website.
Visit PROJECT TREEETEL supports partners’ sustainability programmes
ETEL works closely with its tyre manufacturer partners on a range of innovative and long-term sustainability projects committed to reducing the environmental impact of tyre use. From PROJECT TREE to bringing the newest green technologies to market, ETEL is at the forefront of stocking, wholesaling and retailing the latest tyre technology for B2B and B2C applications.
For example, ETEL was the exclusive UK launch partner for the new Continental ContiRe.Tex range of consumer-focused tyres, manufactured using nylon components made from up-cycled PET plastic bottles. Using recycled materials in the design, development and production of premium tyres helps reduce the overall environmental impact of a tyre’s entire life-cycle.
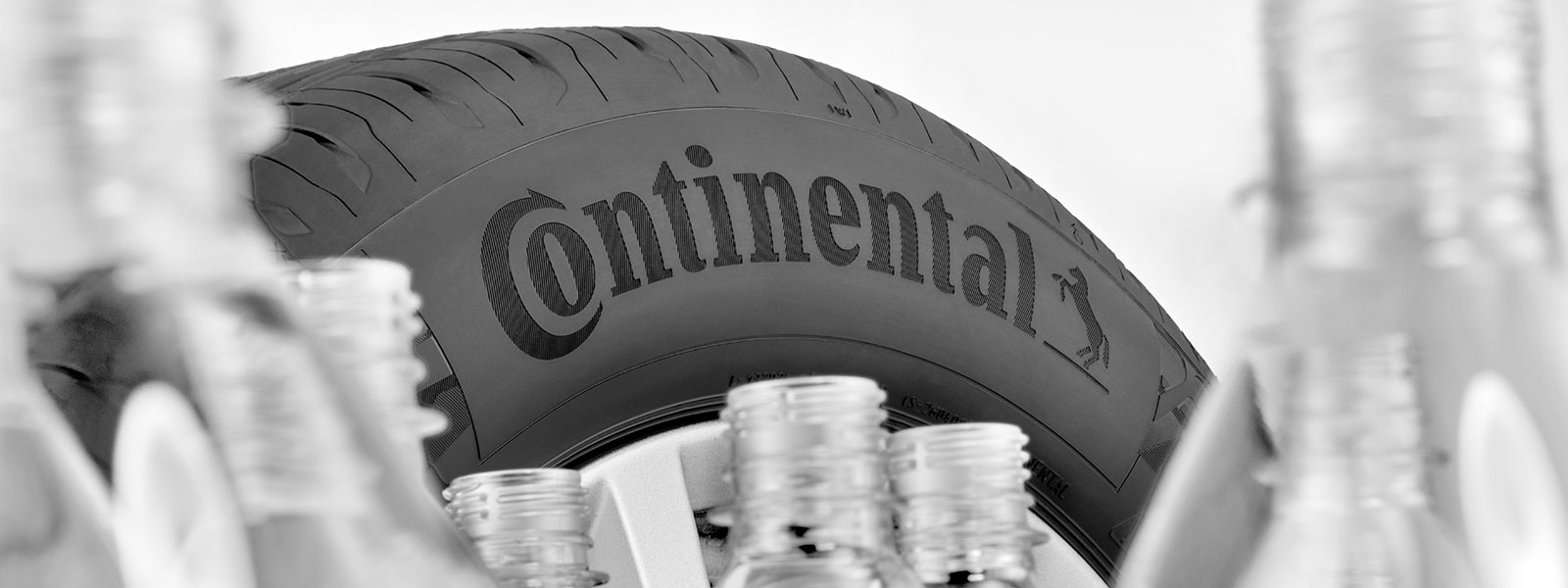
“Tex” is an abbreviation for textiles, in this case, to denote a high-quality polyester yarn produced from recycled polyethylene terephthalate (PET) bottles, which could otherwise have ended up in garbage incinerators, oceans or landfill.
The yarn is mechanically produced without any intermediate chemical steps. The process entails manually separating bottles from the caps, followed by mechanically cleaning, shredding, and processing the plastic into granulate, which is finally spun into the polyester yarn used to make sustainable tyres.
A set of ContiRe.Tex standard passenger car tyres uses material from roughly 40 recycled PET bottles (Between 9 to 15 PET bottles are used per tyre, depending on the tyre size).
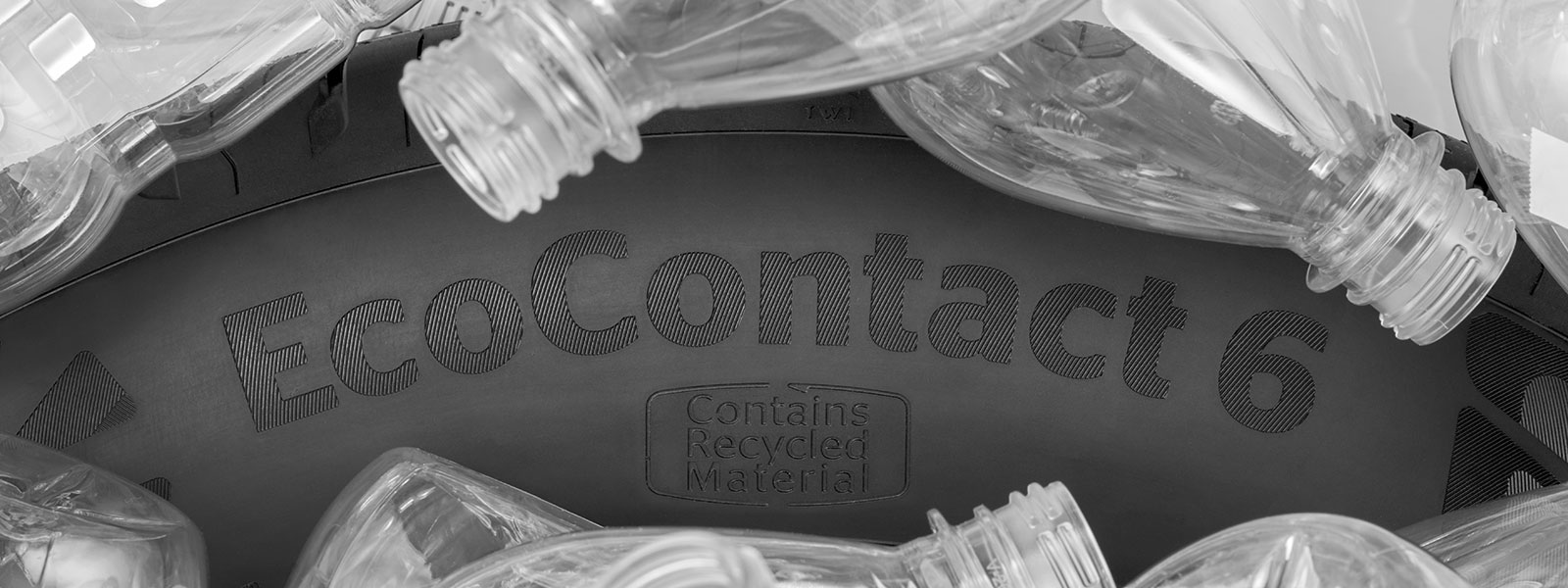
This is just one example of the way ETEL works with our partners to give our customers both B2B and B2C the latest choices for a more environmentally conscious mobility.
Suppliers
As a market leader, ETEL insists on the highest possible standards from its suppliers. This not only applies to the quality and performance of the products it buys, but also the overall corporate behaviour and governance of those with which it has commercial agreements.
In regard to the product quality, ETEL assesses suppliers and their products based on a range of criteria including: Visibility of origin of raw materials; control of end to end manufacturing processes, including adherence to documented quality control procedures; mirroring processes of original equipment where applicable, for the aftermarket; demonstration of supplier research and development capabilities; and adherence to all relevant legislation. Critically, suppliers need to demonstrate an ongoing product testing programme is in place and share the results of those tests.
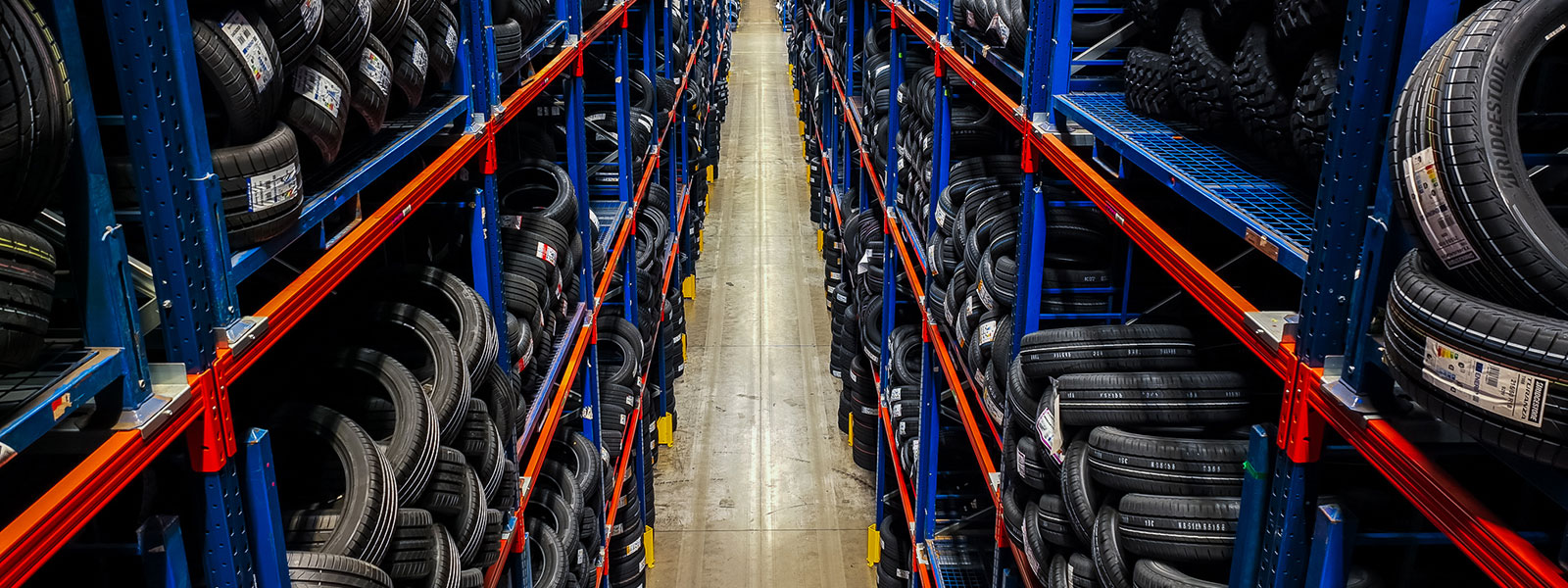
When it comes to governance, suppliers must demonstrate compliance in areas such as modern slavery, human trafficking and child employment law. Factories must demonstrate proper use of PPE and adherence to health and safety protocols as well as being able to provide certification for the full traceability of their products, including waste management. ETEL carries out regular inspections of supplier sites and will change supply routes or even withdraw contracts if suppliers and products fail to meet the standards required.
ETEL Logistics
ETEL operates a national distribution network designed to transport products as efficiently as possible and reduce ‘wasted’ journeys. Vehicles delivering new tyres to retail centres pick up the used tyre casings and return them to our hubs for reprocessing, thus cutting down on the number of journeys required and reducing the fuel needed.
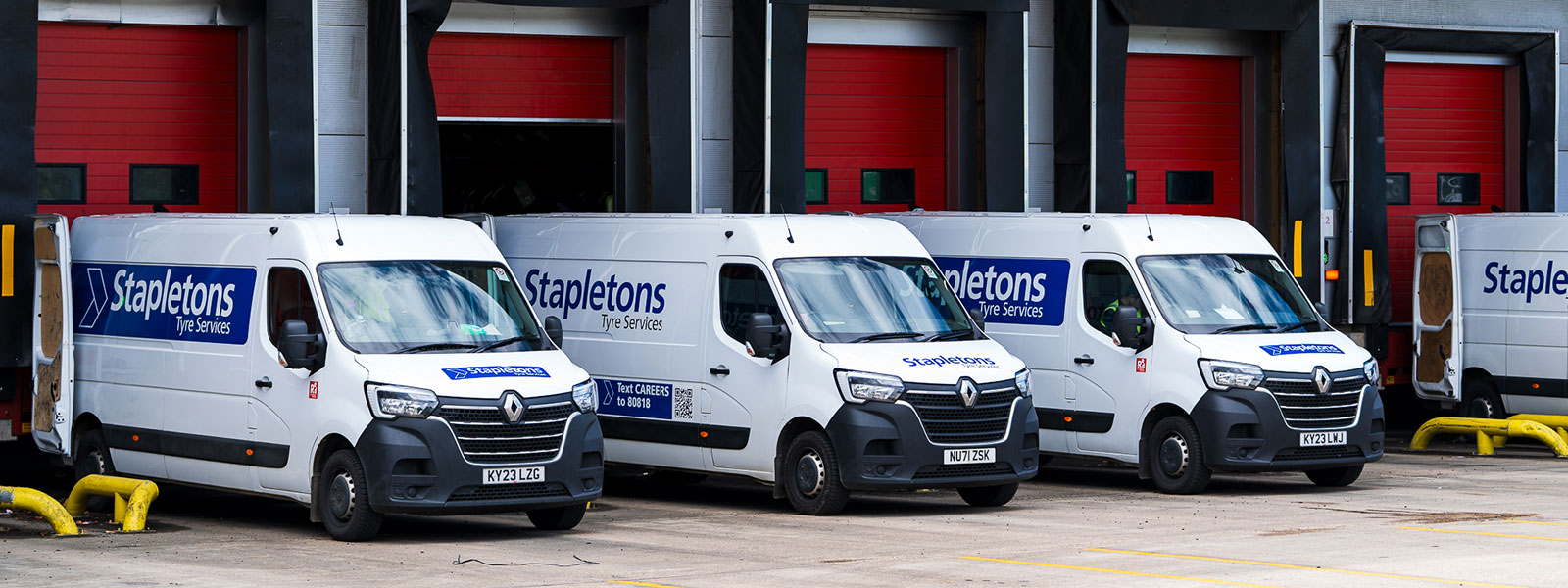
Using the same vehicle to deliver new and collect used tyres in the same visit significantly reduces the miles travelled, thus reducing fuel used and CO2 emissions. This process became even more seamless with ETEL’s acquisition of Murfitt’s Industries, the leading tyre recycling company in the UK.
ETEL operates 11 stand alone distribution sites that take as many deliveries as possible directly from suppliers’ manufacturing sites in order to remove doubling handling and unnecessary journeys from suppliers’ UK distribution centres. Our distribution sites are strategically located throughout the UK, enabling ETEL to be as close to the customer as possible, with this national presence reducing the amount of mileage required to be covered.
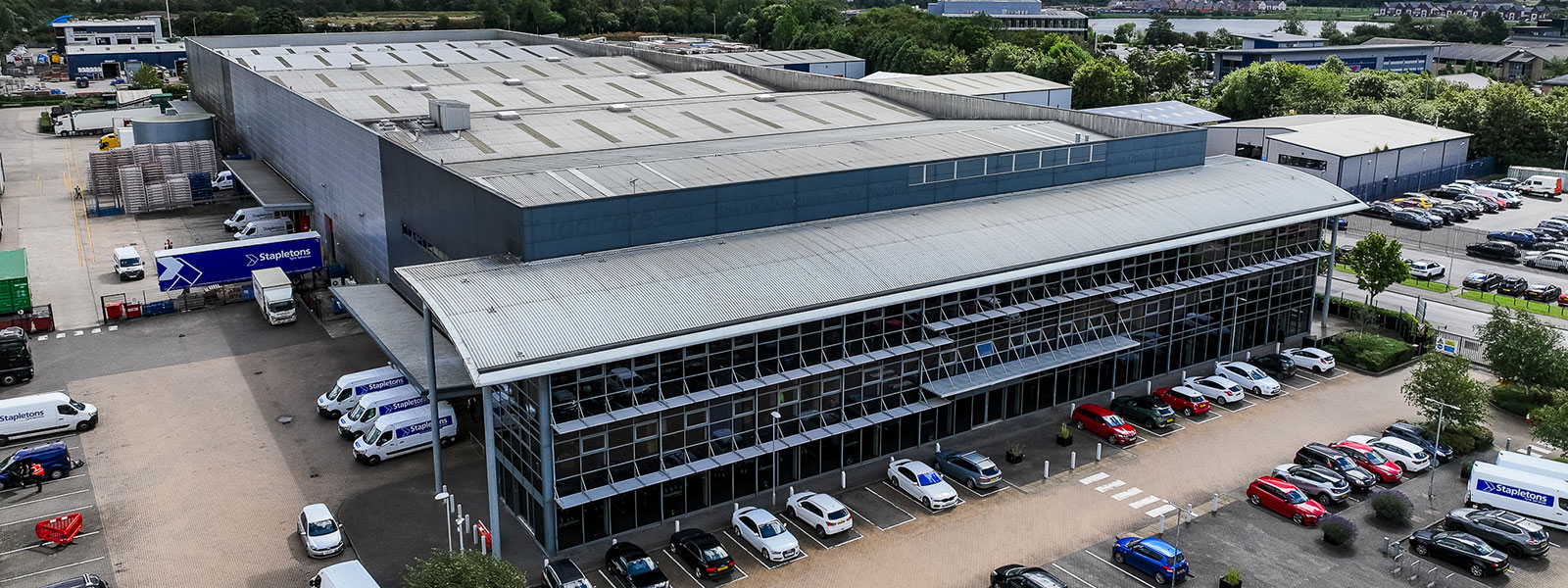
Fuel consumption in our transport operations accounts for the largest proportion of our energy use. ETEL is testing the use of electric vehicles within its overall fleet although as yet, there are not viable EV options available for the bulk of its deliveries or for the mobile fitting fleet. However, EV and Hydrogen technology in the commercial space is advancing and we are hopeful that zero emission options will become available in the medium term.
In the meantime we are investing heavily in the latest technology to allow for the most efficient driving and delivery routing of our current vehicles. We have a full telematics system installed on every ETEL commercial vehicle which allows us to track, by driver and vehicle, how the vehicle is being driven. This allows us to maximise fuel efficiency/reduce wear and tear through driver programmes of education, training and recognition. We have an ongoing review programme which interrogates our route planning which enable us to continually reduce delivery miles through more efficient routing and execution.
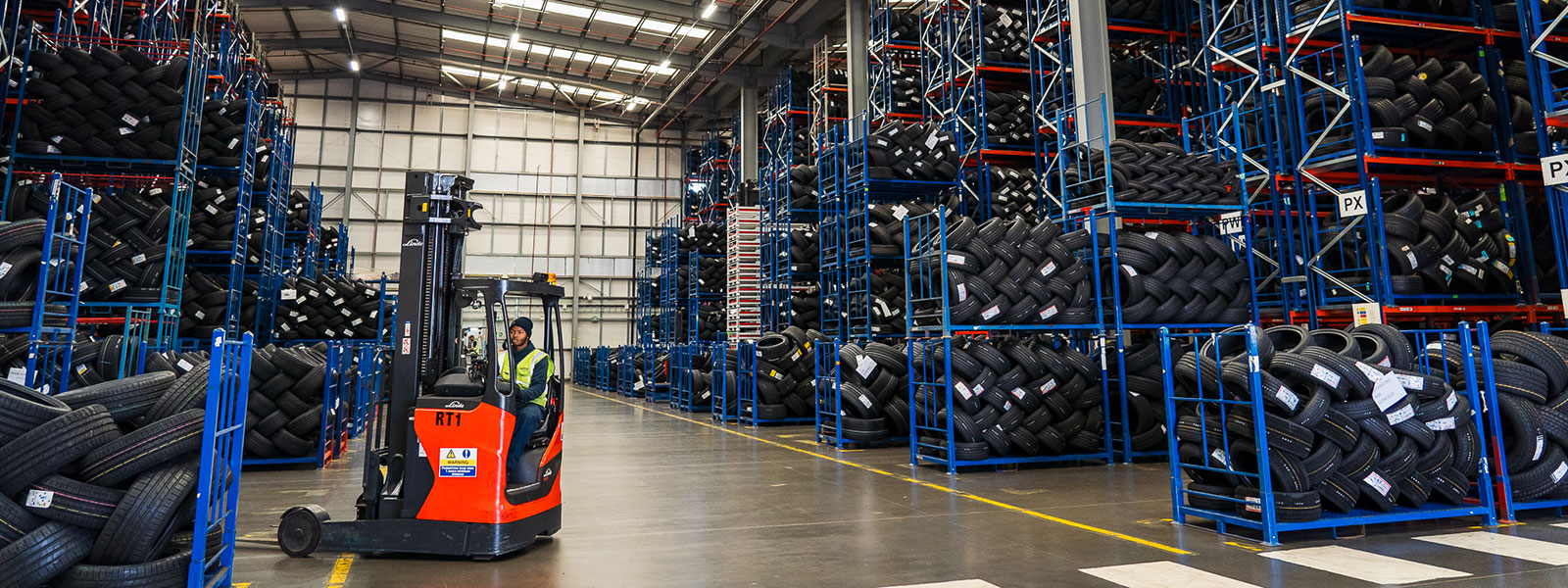
Within our warehouses we have converted all lighting over to the most energy efficient lighting. These work in conjunction with sensors that automatically switch all lighting on/off depending on whether someone is working in the area. We also operate a large fleet of forklifts and look to replace these with the latest energy efficient Lithium Ion battery forklifts as they reach the end of their life.
We are constantly focused on reducing our energy usage, the majority of which is electricity in our premises and fuel for our commercial fleet, but also includes gas consumption and power for other vehicles.
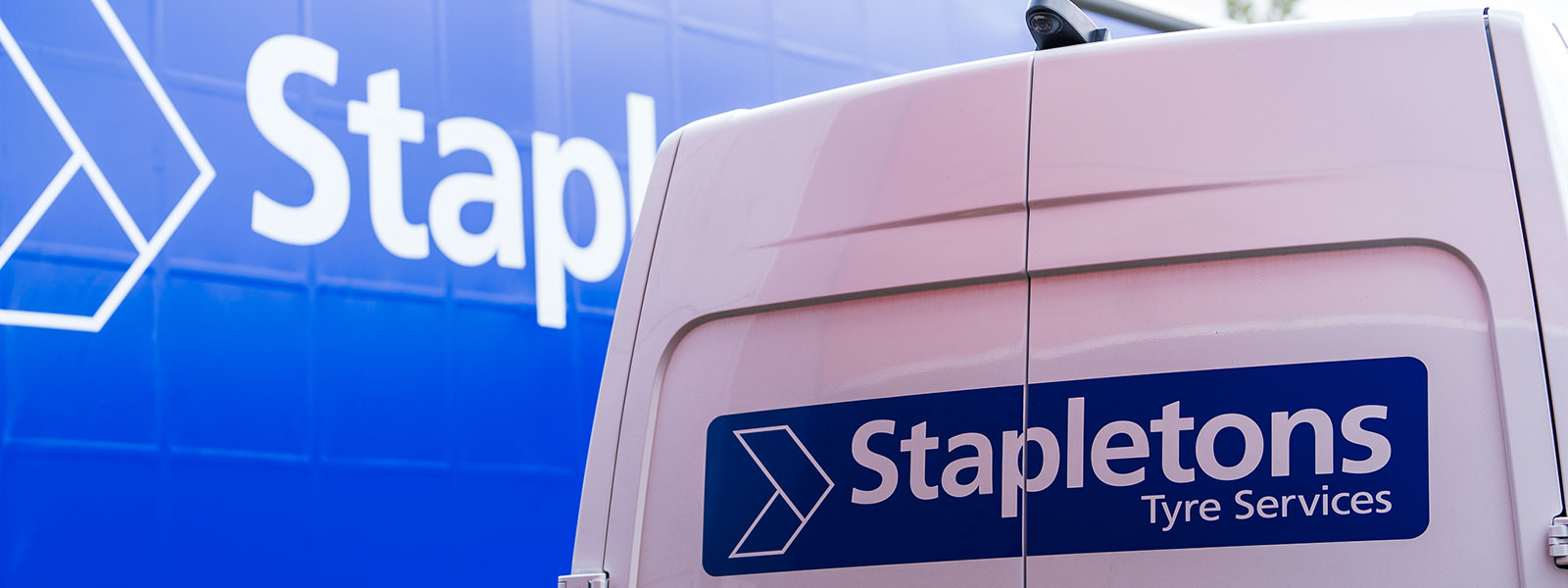
Our overall energy consumption in our last full year (2021/22) rose by 2.8% on the previous twelve months. This reflects the difference between a lower level of activity during the pandemic and a period which included some post Covid recovery. The difference is accounted for by the increase in commercial vehicle journeys during the last year - which is partly offset by our increased efficiency in use of electricity and gas. For context, our like-for-like UK sales rose by 18% over the same period.
We are currently developing our Climate Roadmap to establish time-bound specific goals for our Group against which we will continually measure our progress.
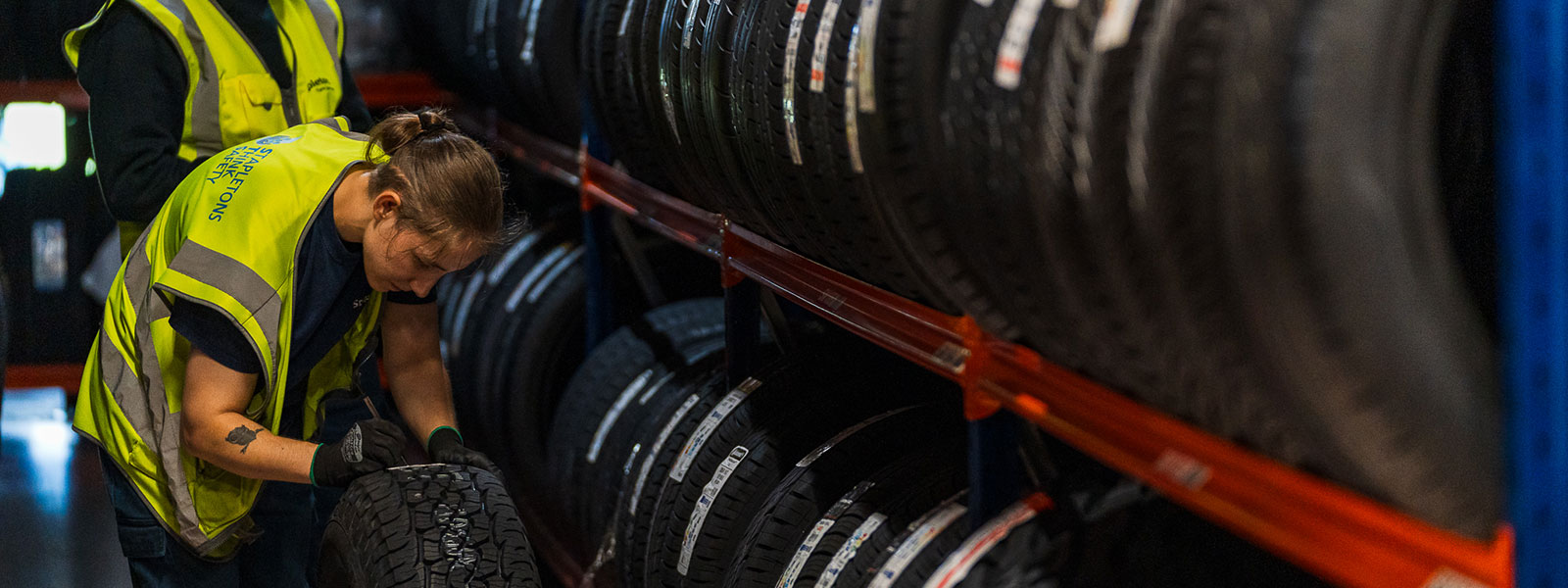
Centre Activity
The primary objectives of our centres are to ensure our customers are safe on the roads and that their cars are running as efficiently as possible. Minimising the environmental impact of motoring goes hand in hand with reducing costs, from ensuring tyres have as long a life as possible, to keeping engines running to maximum efficiency through regular servicing.
By holding the largest tyre stock in the UK, ETEL ensures that drivers have access to the right tyre in the right place at the right time. This is increasingly important as the car parc shifts towards electric vehicles with tyre choice playing a significant role in maximising the range of EVs – and therefore minimising energy usage per mile.
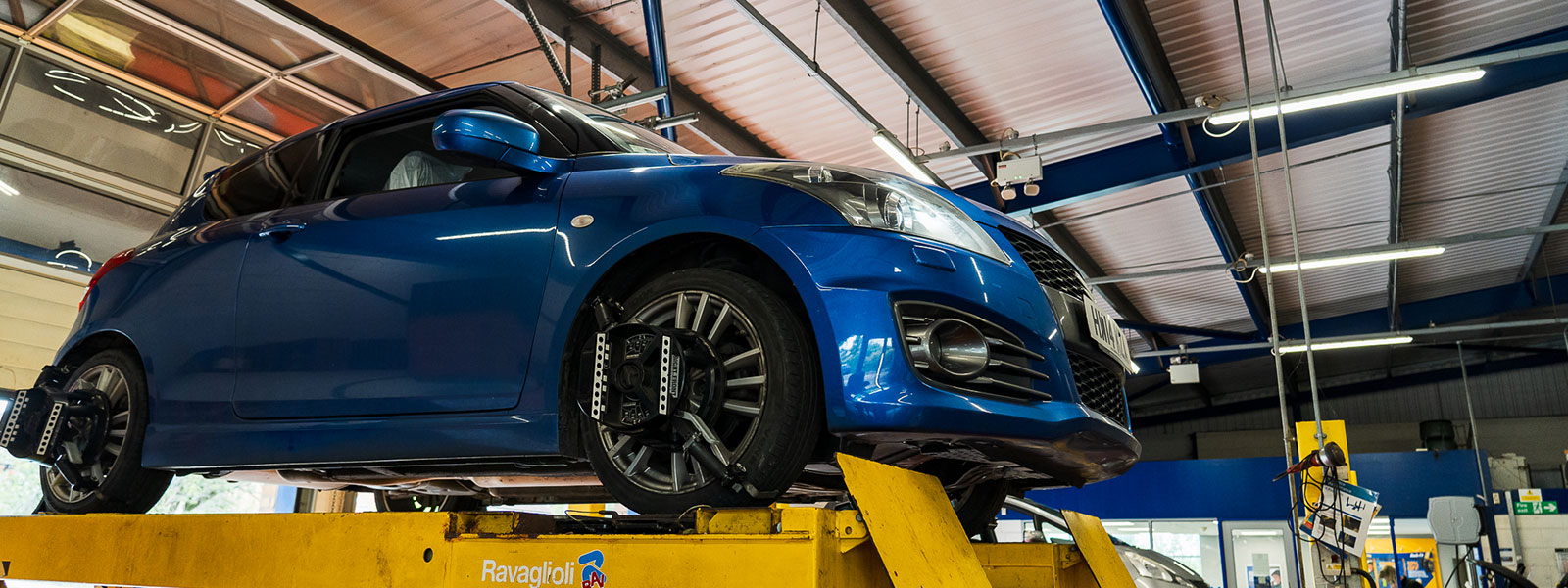
As the proportion of EVs in the UK car parc increases, more data is becoming available and ETEL can provide greater guidance on the importance of correct tyre choice for EVs.
ETEL provides its staff with industry leading training, equipping its centre teams with the knowledge and skills they need to advise their customers on the best tyre choice for their needs, as well as the importance of ensuring vehicles are running with the appropriate tyre pressures. Correct tyre pressure is not only vital for the tyre to deliver its road holding potential, but also in minimising tyre wear, reducing both environmental impact and cost per mile.
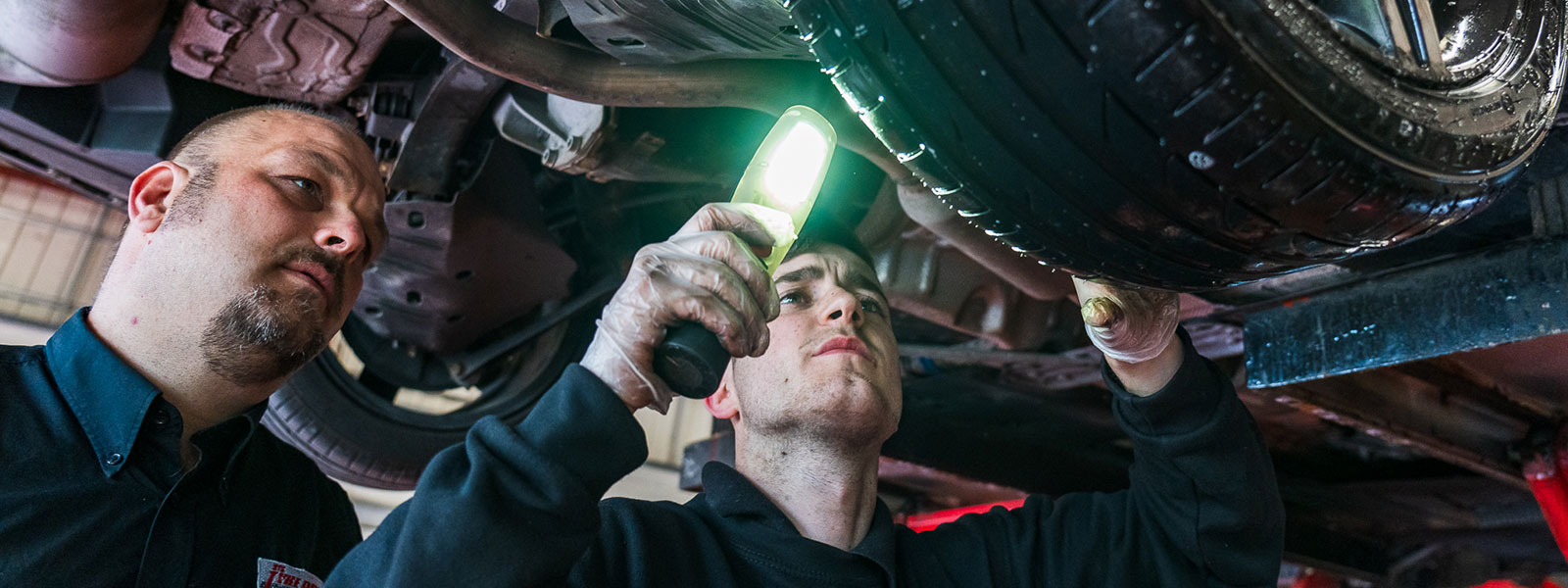
Not only is the appropriate pressure vital in prolonging tyre life, having the correct wheel alignment will also maximise longevity. ETEL staff are trained in identifying wear patterns which indicate misalignment and in using the centres’ laser alignment technology which ensures vehicles can re-set to the manufacturers’ recommendations.
Product recovery from centres
Of course, however efficiently a car is run, there will come a point when some components need to be replaced, and at this point it is vital that the used products removed for a vehicle are re-processed responsibly and as much material recovered as possible.
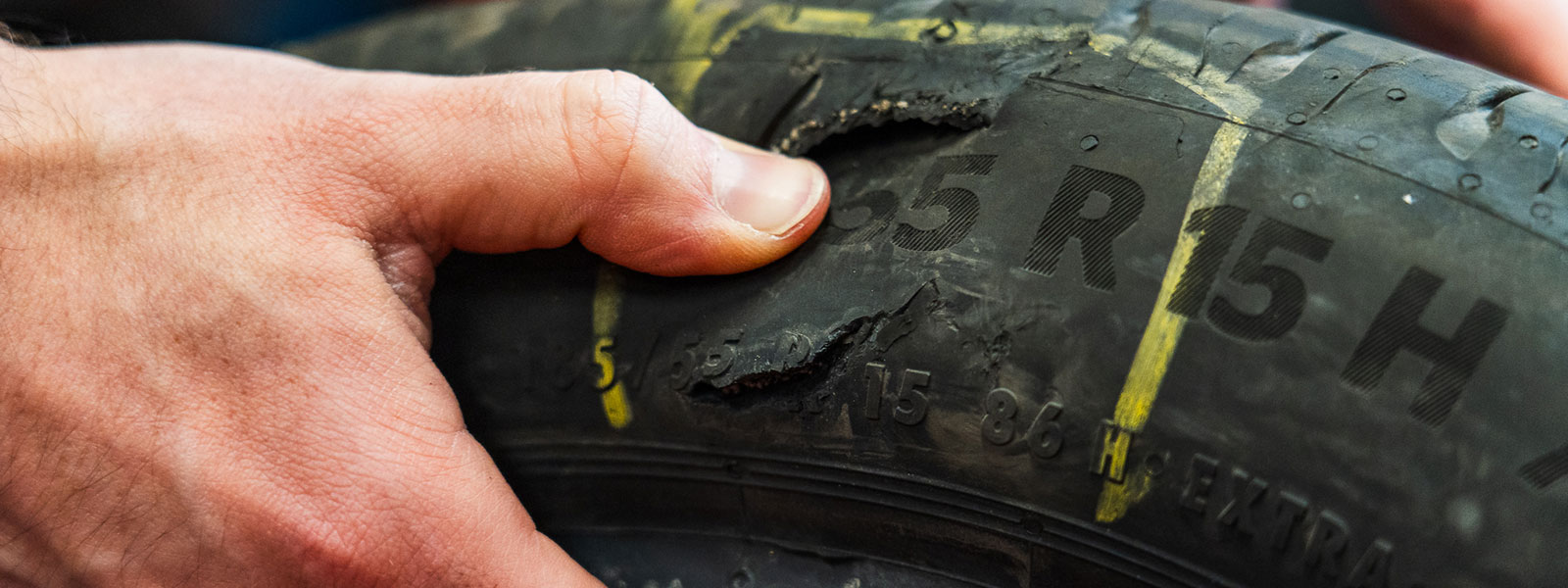
ETEL works with responsible waste management companies to re-process used products including: tyre casings, exhausts, shock absorbers, brake parts, spark plugs, zinc balance weights, catalytic converters, batteries, oil and oil filters, air filters and anti-freeze, as well as general waste.
Around 1,750 tonnes of used metal are collected each year from ETEL locations, primarily our retail centres. The metal is processed to ensure that none of our metal waste is sent to landfill. Scrap catalytic convertors are recycled to extract the precious metals - platinum, palladium and rhodium - from the old cores, which are then processed to be re-used in new products.
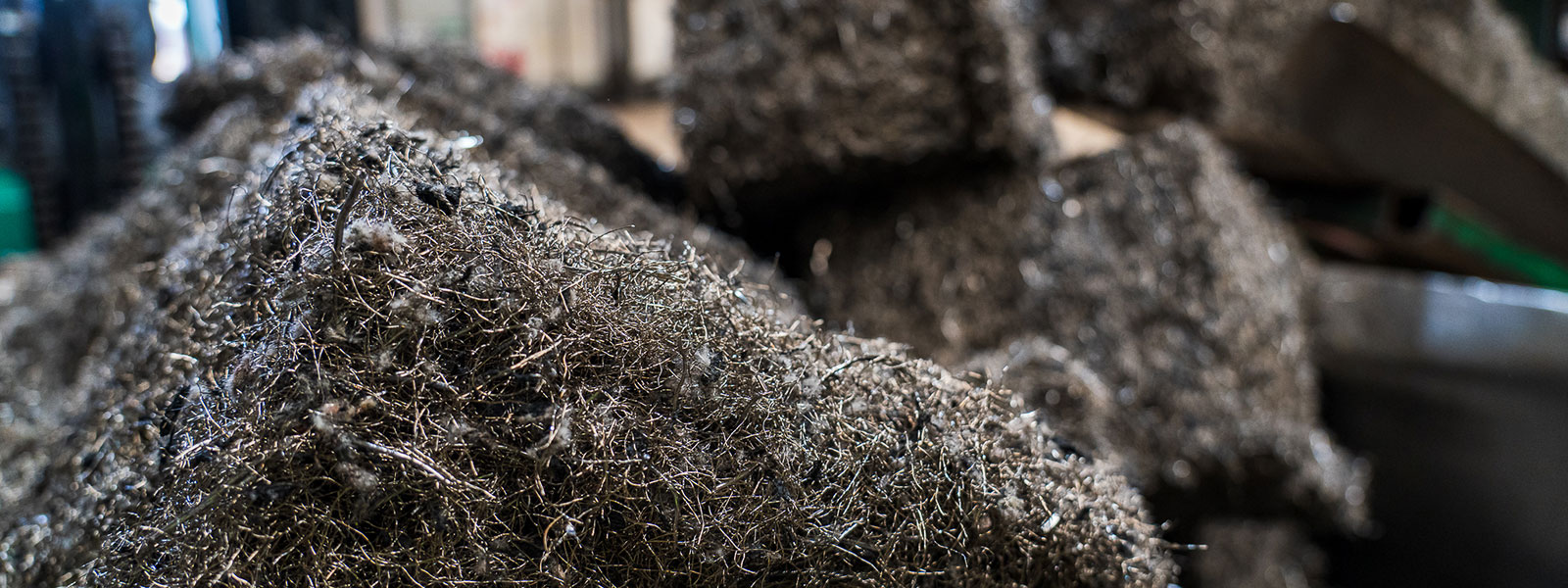
The core of some components can be reused to remanufacture new replacement parts. Every year we return around 25,000 units to our suppliers. Of these approximately 80% are brake caliper cores, with the remainder comprising items such as alternators and drive shafts.
Approximately 70,000 scrap car batteries are collected from our centres every year for recycling, with 97% of the content of those batteries being reused. The lead from the batteries goes into the manufacture of new batteries as well as to the construction industry for use in flashing for roofs.
We drain over one million litres of waste oil from customers’ vehicles each year. Although this oil is no longer able to perform to the original standards in lubricating engines, it still has value. 93% of that oil is recycled into fuel oil. The used oil filters are also reprocessed, with the waste oil extracted and the metal shredded and recycled.
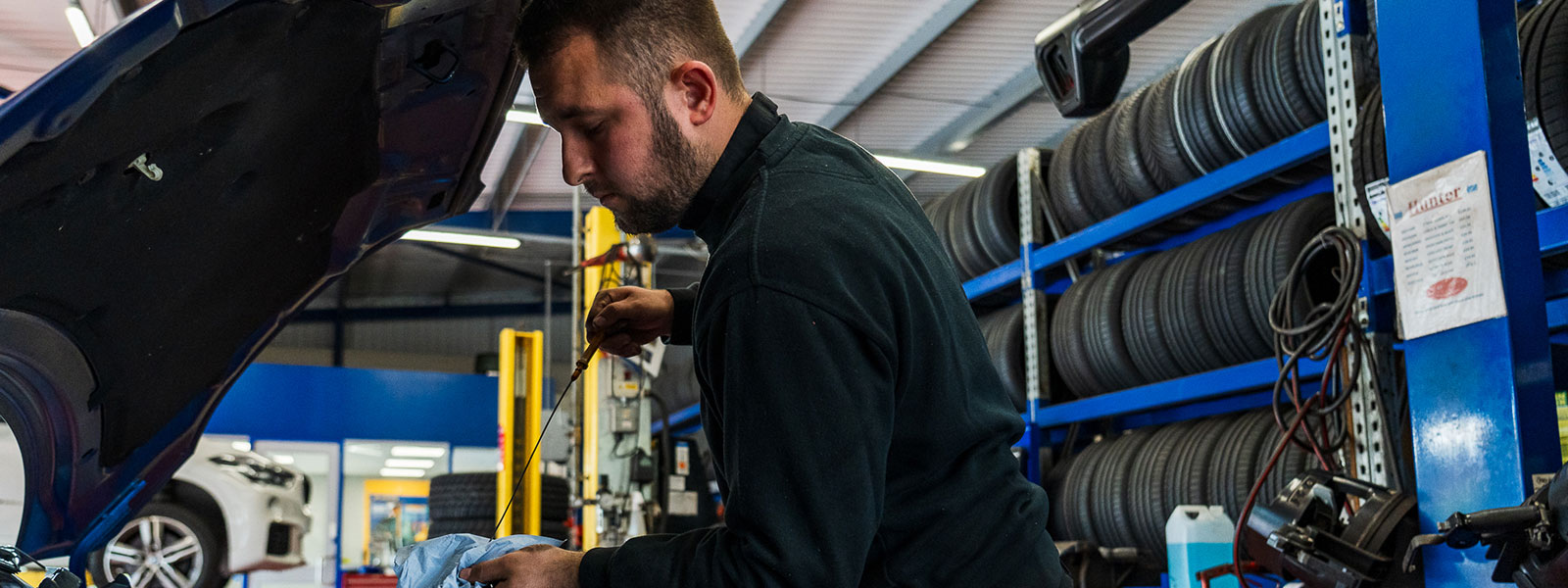
60% of our waste anti-freeze / coolant is recovered for bacterial treatment at sewage farms with the gas created by the digestion process used to generated electricity. Our absorbent waste is also used to generate electricity - 95% of this material is recovered and burnt under controlled conditions to generate power which is fed back into the National Grid.
Around 64% of the 2,500 tonnes of general waste produced annually by ETEL is recycled and therefore avoids landfill.
Tyre Recycling
Within the ETEL group is Murfitts Industries, the country’s leading tyre recycling company, which operates a national network recycling the equivalent of around 20 million car tyres per year.
Murfitts manufactures a variety of rubber granulate products by processing and repurposing post-consumer tyres which it collects from a wide range of tyre manufacturers, wholesalers and retailers across the UK, not just those tyres replaced at Kwik Fit centres.
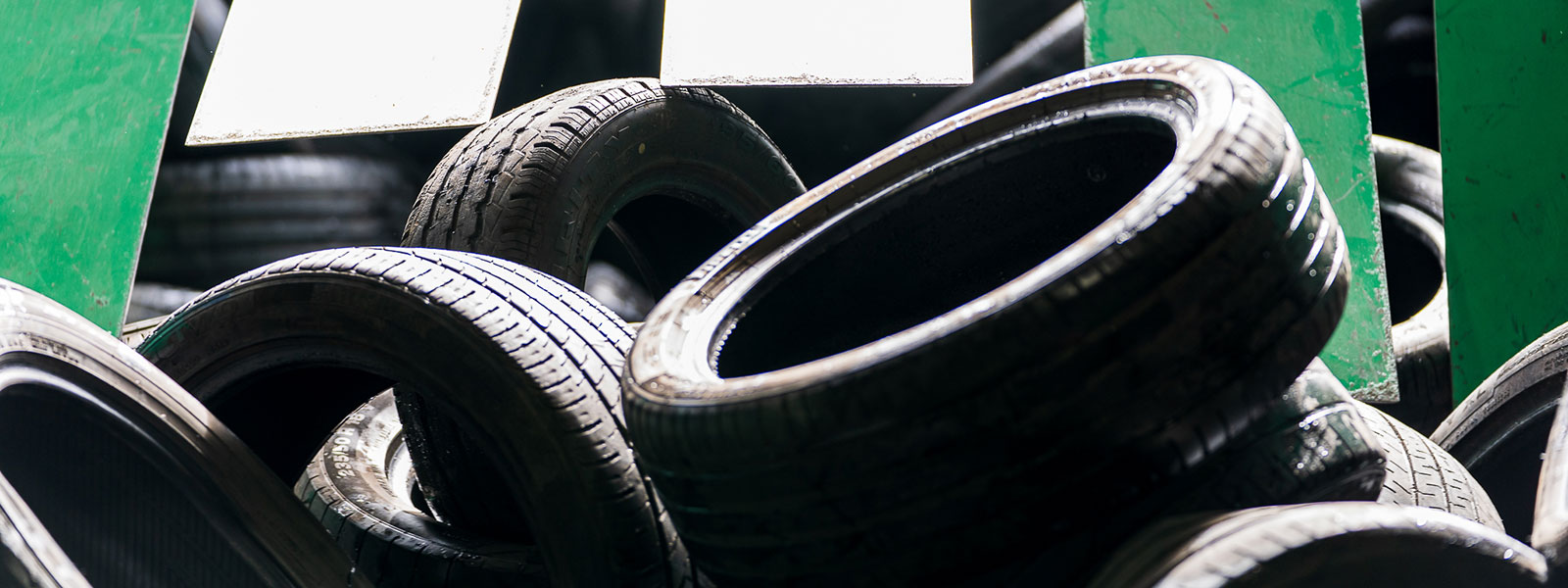
By offering the responsible collection, processing and re-manufacturing of tyre material within the ETEL group, customers - both retail and wholesale - can be confident that their used tyres are being processed in the most sustainable way possible.
Wherever possible, used tyres are collected on the same journeys as the delivery of new tyres to centres. Once back at ETEL’s distribution hubs, the used casings are shredded to reduce their volume and cut down even further on the number of journeys required to transport the used rubber to Murfitts re-processing centres.
Murfitts has invested significantly in its processes, developing a sophisticated system which enables it to recover the materials used in the production of tyres and repurpose them to manufacture innovative products. These are used in areas such as sports surfaces, pathways, children’s playgrounds, carpet underlay, modified asphalt and many other industrial applications. Its products are of such high quality that they are exported to markets across the globe.
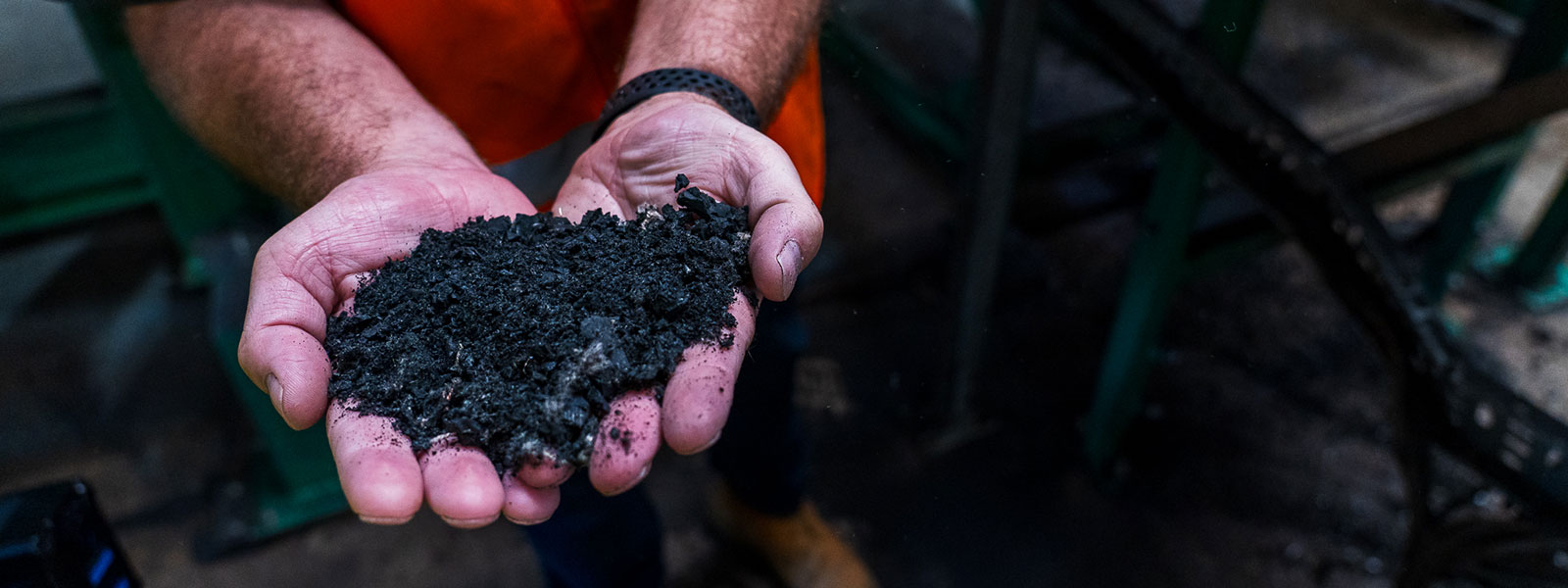
Murfitts continues to develop its rubber crumb products with innovations adding commercial value through delivering premium performance. Its hybrid sports pitch infill, PRO-gran, not only helps reduce heat absorption, but also delivers other significant benefits. The polyurethane coating results in pitch performance being improved, skin abrasions reduced by up to 25% and the infill releasing no airborne particulates or micro plastics.
PRO-gran passes the Dutch Soil Quality Decree, one of the world’s leading policies on sustainable soil management. Murfitts is continually expanding the range of products under the PRO-gran brand, which is now used in leading sports pitches in countries across the world.
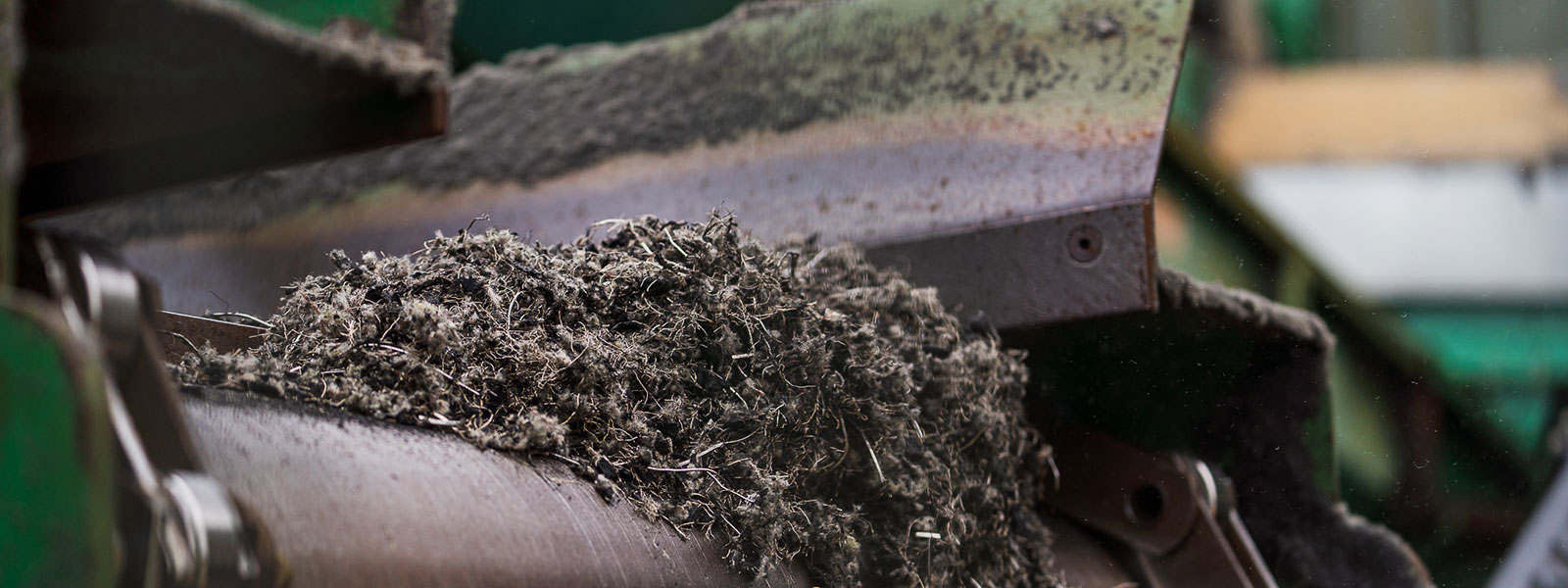
Over the last decade Murfitts has introduced processes ahead of, and exceeding, UK regulatory requirements regarding the disposal of post-consumer tyres. It has led the industry in developing audited and traceable systems to ensure tyres are being processed responsibly. Recognising the global focus on the reduction of waste and the need to support the circular economy through the re-use of materials, Murfitts has also been investing in research and development to improve material recovery and reduce the use of natural resources.
The company has been developing proprietary pyrolysis technology, a thermochemical process used to decompose the tyre feedstock at high temperatures in a vacuum into various high-value recycled materials such as carbon black and recycled fuel oil. The aim of developing this programme is to help improve the sustainability initiatives of the tyre industry even further by replacing one of major raw materials of tyres, carbon black, with a recycled product.
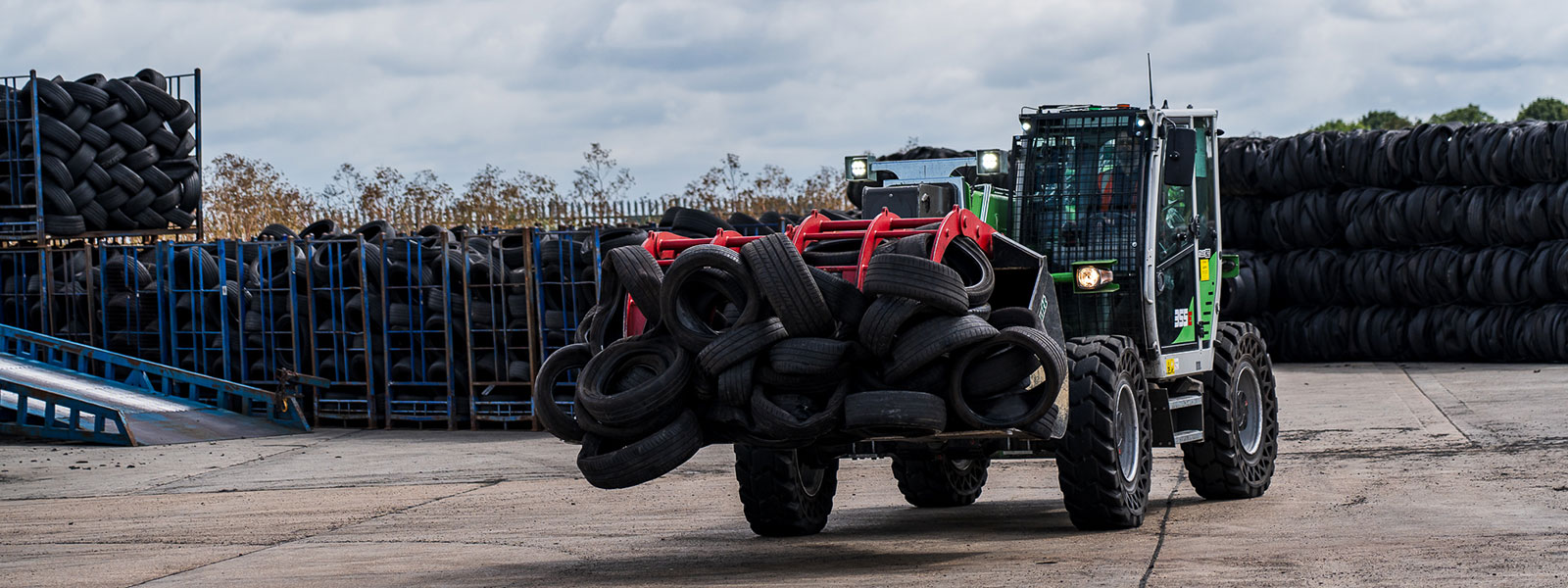